At its core, CNC milling includes the elimination of product from a workpiece via a series of collaborated activities. The procedure begins with the layout of a 3D version using computer-aided layout (CAD) software. This model functions as the blueprint for the milling device. As soon as the design is completed, the driver makes use of computer-aided manufacturing (CAM) software application to convert the CAD model into a set of guidelines that the CNC machine can check out, usually in the kind of G-code. This code dictates the motions of the maker's cutting devices, such as spindle rotation and feed prices, making certain that every cut is precise and replicable.
One of the standout features of CNC milling is its adaptability. Unlike conventional milling machines, which normally operate along one or 2 axes, CNC milling makers can operate on numerous axes at the same time-- commonly 3, 4, or also 5.
Check out cnc milling guide the transformative world of CNC milling, an innovation that combines accuracy and automation to create high-quality parts effectively from different products, and find its processes, benefits, and key factors to consider for success in modern production.
The choice of devices is another essential element of CNC milling. There is a variety of cutting devices available, consisting of end mills, face mills, and ball mills, each fit for various applications. End mills, for example, are versatile devices that can be used for side and face cutting, while round mills are perfect for developing rounded edges and complex contours. The appropriate tool option can significantly influence the quality of the completed item and the efficiency of the machining procedure. In addition, appropriate device upkeep and condition surveillance play a significant duty in preserving optimum performance and extending device life.
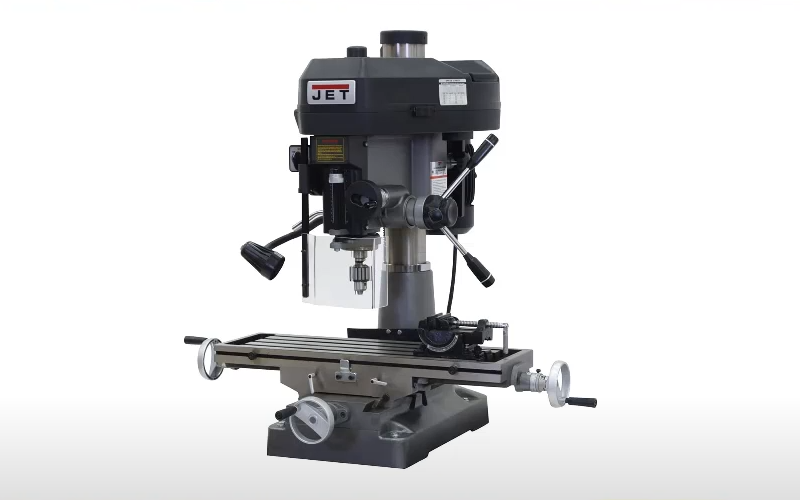
One crucial variable to consider in CNC milling is material compatibility. Comprehending the buildings of the product, including its hardness, machinability, and thermal conductivity, allows operators to optimize the milling process and accomplish remarkable outcomes while decreasing wear and tear on devices.
Past the technical elements like style, tooling, and materials, there are extra factors to consider for maximizing CNC milling procedures. Job planning is important, as it includes whatever from maker option and arrangement to organizing and operations monitoring. Reliable work preparation can cause greater performance, minimized preparations, and boosted general efficiency. Using sophisticated functions such as toolpath optimization methods can improve the milling process even more, making it possible for much faster machining cycles and lowering waste.
One of the significant benefits of CNC milling is the ability to automate repetitive jobs, which minimizes human error and improves production consistency. While typical milling devices need an experienced operator to manage the manufacturing process, CNC milling machines can run ignored, implementing pre-programmed guidelines with precision. This level of automation not just boosts efficiency but likewise releases up skilled workers from mundane tasks, permitting them to concentrate on better activities such as quality assurance and procedure improvement.
Regardless of its benefits, transitioning to CNC milling is not without obstacles. The accessibility of leasing choices and economical entry-level CNC milling devices has made it extra obtainable for tiny and mid-sized services to adopt this technology.
Training and ability advancement for workers operating CNC milling machines are additionally necessary for making best use of the return on financial investment. Operators need a strong understanding of both the CNC equipment itself and the software program being utilized for programming and monitoring. Several makers discover success by providing internal training programs or partnering with outside training organizations to outfit their groups with the required skills and expertise.
Recently, technological innovations proceed to shape the area of CNC milling. As sectors progressively turn to automation, incorporating functions such as synthetic knowledge (AI) and machine understanding into CNC machines can better enhance the precision and performance of milling operations. Smart CNC systems, which include sensing units and data analytics, can monitor efficiency in real-time and make instant adjustments to enhance machining parameters or to recognize deterioration on tools. This data-driven technique holds the prospective to dramatically decrease downtime and maintenance prices while enhancing general productivity.
Improvements in software application are constantly narrowing the void in between style and manufacturing. Modern CAD/CAM systems now provide extra instinctive user interfaces and enhanced simulation abilities, allowing drivers to picture machining processes before they are performed. By detecting potential issues in the design phase, firms can resolve design imperfections or maximize reducing methods without incurring expensive alterations to physical products.
In the context of CNC milling, sustainability is likewise acquiring significance as manufacturers seek methods to decrease their ecological effect. Executing techniques such as enhancing cutting criteria, using extra effective tooling, and recycling products can contribute to a more lasting milling operation. Furthermore, technologies such as additive production are being explored combined with CNC milling, providing possibilities for hybrid manufacturing techniques that further enhance sustainability by lessening waste.
Explore benchtop milling machine the transformative world of CNC milling, an innovation that incorporates precision and automation to create top notch parts efficiently from various materials, and find its procedures, benefits, and crucial factors to consider for success in modern-day production.
In verdict, CNC milling stands for a crucial property in modern-day manufacturing, offering business with the capability to produce complex and high-grade parts effectively. Its combination of flexibility, automation, and precision has made it a staple in sectors ranging from aerospace to auto, medical to customer items. Comprehending CNC milling starts with a strong structure in its procedures, including the interplay in between design, tooling, materials, and software program. As technology continues to progress, the possibility for competent drivers to utilize these advancements will only broaden, permitting better performances and innovations in CNC milling applications. By staying informed on ideal techniques and arising modern technologies, suppliers can place themselves at the center of this vibrant market and completely make use of the abilities that CNC milling provides. Ultimately, successful combination of CNC milling equipment, skilled workforce training, and wise automation leads the way for the future of manufacturing, where performance, sustainability, and high quality end up being the characteristics of operational quality.